はじまりは、
日米両社の出会いから。
追いつき、追い越せ。
モータリゼーションの興隆が押し寄せた昭和40年代。日本の自動車産業には明確な目標があった。技術的に大国アメリカから学ぶべきことはまだまだ多く、憧れから模範に、そしてライバルへと、その関係が移り変わる激動の時代だった。そんな中、当社が生まれる。まさしくアメリカの力を借りてである。
大豊精機誕生のきっかけは、1970年、自動車部品製造の大豊工業が、アメリカのプレス用金型・自動化装置の製造会社「リバノイスオートメーション社」と販売契約を交わしたことによる。自動車産業の発展に寄与できる新たな分野を模索していた大豊工業は、プレス工程の自働化に着目したのである。
さっそく開始された営業活動では、約4億円に達する引合額があり、市場としては有望であった。リバノイス社の技術的指導があれば、既存設備を応用してリバノイス製品よりも約30%程度安く製作できると判断した大豊工業は、新会社設立を決断。1973年、リバノイス社との合弁で、当社の前身「大豊リバノイスオートメーション」が発足した。
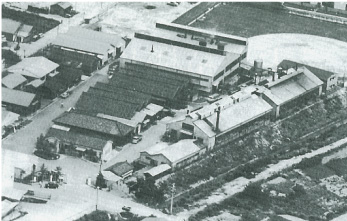
当時の大豊工業
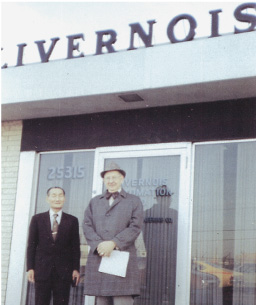
リバノイスオートメーション社
合弁終結から社名変更へ。
翌1974年から、プレス用金型の設計製作・販売を開始。1978年にはプレス内搬入・取り出し装置の新製品を開発・販売。リバノイス社の技術を短期間で修得するとともに、少しずつ業容を広げて発展の道を歩み始めた。
そして同年11月、体制整備に伴い、両社の合弁契約を終結。社名を「大豊精機株式会社」とし、独自の技術力を携え、新たな船出となったのである。
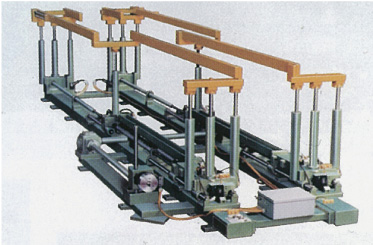
リバノイス社製コンパクトプレス搬送機
効率化・合理化を推進。
大豊精機誕生後は、一貫して自動車産業のプレス工程における効率化に貢献する道を歩む。1980年から順次、工場や設備を拡充し、生産・加工能力の向上・合理化を進めていった。徹底した効率化追求は、新たな答えも導いた。プレス工程のみでの効率化追求に限界が見えてきたため、プレスの後工程である溶接を含めた合理的な製法を模索。1980年に溶接機・溶接治具の本格生産を開始した。また、新機構による金型交換台車や、プレス内搬入・取り出し装置など、積極的に新製品を開発。こうして、現在の大豊精機の基礎となる姿ができていった。
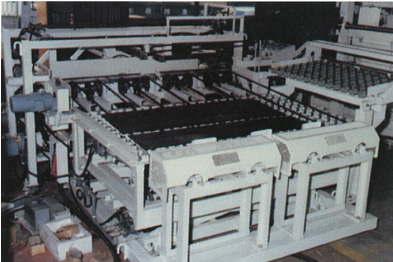
プレス自働化ラインシステムを開発(1980年)
工場拡大と、システム構築。
社員個々の懸命な努力は、業界での認知を確実に高めていった。会社の規模も徐々に拡大。1985年に第1工場が緑ヶ丘へ移転し、金型工場として稼働を開始。1988年には本社兼第2工場を併設し、開発・試作部品を担当。続いて同年、機械加工工場としての第3工場も新設された。さらに1996年、鞍ヶ池工場を新設し、搬送装置・溶接機の設備組立工場に。技術的にも実りある時期を迎えることとなった。
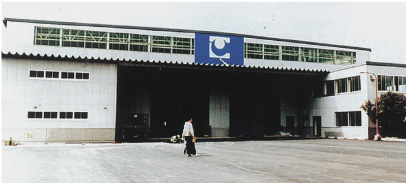
第1工場(旧:本社第1工場 現:ガスケット本社)
常識を覆すプレス設備、
「コンパクト・ハイドロフォーミング」「パイプ液封成形技術」の開発。
時代はミレニアムを越え、自動車に対するユーザーニーズの多様化はさらに進み、生産現場へも効率化追求の波として押し寄せていた。
そんな中、トヨタ自動車との協同開発で「コンパクト・ハイドロフォーミング」の実用化に成功。これは従来のハイドロフォーミングの常識を覆すもので、金型を含め、前後の工程をシステム化。サイズと消費エネルギーが従来機の1/10、コストは1/2、さらに中間在庫0を実現した画期的な技術だ。
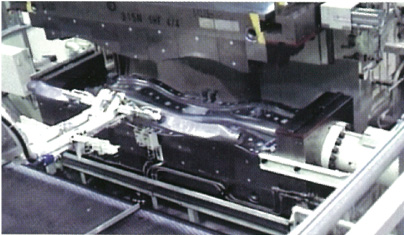
コンパクトハイドロフォーミングマシン
次に取り組んだのは「パイプ液封成形技術」。従来、プレス成形した数点のパーツを溶接して仕上げていた製品を、パイプに封入した液体の反力を応用し、小型のプレス機で一度に成形できる革新的な技術で、製品の強度向上と、製造工数低減を両立することができた。
このコンパクト・ハイドロフォーミングとパイプ液封成形技術によって、2002年・2003年と、連続してトヨタ自動車「技術開発賞」を受賞した。設備製造会社がこの賞を受賞することは稀であり、それを2年連続で受賞できたことは、長年、技術力を培ってきた努力が報われた瞬間であった。
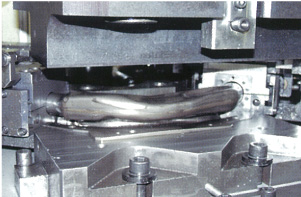
液封技術によるプレス加工
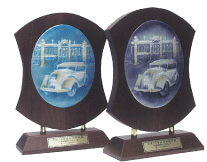
「技術開発賞」の盾
量産部品事業へ進出。
トヨタ自動車が元町工場で液封成形によるロアーアーム製造をスタートさせた後、「自らの設備で量産部品をやってみないか?」と打診された。当社にとって、念願の量産部品事業への進出である。さらに、それだけにとどまらず、お客様と同じ立場で製造設備の評価が可能となり、設備の完成度をさらに高められる。
与えられた課題は、新型ミディアムカーのサスペンション部品。部品事業部を設立し、2004年、鞍ヶ池工場で生産を開始した。
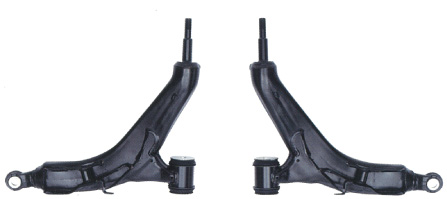
当社初の量産部品となったフロント・ロアアーム
天津大豊精機
汽車設備有限公司を設立。
そして同年5月には、中国・天津市に、当社100%出資の海外拠点「天津大豊精機汽車設備有限公司」を設立。
中国という巨大市場を舞台に、最適調達・原価低減を通して、お客様のグローバル展開に貢献することとなった。
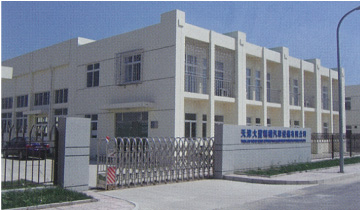
当社初の海外生産拠点、天津大豊精機汽車設備有限公司
「新生・大豊精機」始動。
量産部品事業への道筋が明確になったことで、新たな拠点づくりが急務に。そのため、2004年7月に「花本産業団地」への進出を決定。2005年5月には、生産ラインが鞍ヶ池工場から移設され、本格的に部品製造がはじまった。
この花本工場は、当初、量産部品棟とプレス棟の建設計画で進められていたが、花本という地の利と、そのゆとりあるスペースから、本社も移転すべきと判断。そして11月、多数の来賓を迎え、新本社・本社工場の「竣工披露会」を開催。こうして「新生・大豊精機」の基盤が固まった。
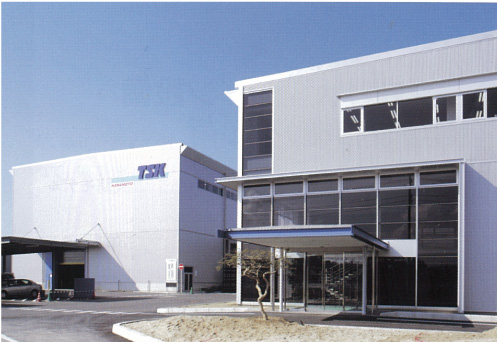
完成した本社事務棟(右)とプレス棟(左)
トヨタ新型車用
アクスルビームの生産を開始。
本社工場の完成とともに、量産部品事業が本格稼働。新型コンパクトカー用アクスルビームの出荷式が行われ、2005年10月にラインオフした。
さらに、2006年1月に発売された、3.5リッター280馬力という国産ミニバン最強エンジンを搭載したトヨタ新型車にも、当社の液封成形によるアクスルビームが採用された。
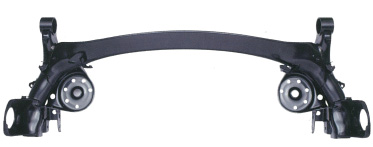
アクスルビーム
コンパクト焼結用プレス機で、
トヨタ自動車「技術開発賞」受賞。
2006年2月、「コンパクト焼結用プレス機」の功績により、当社としては3回目のトヨタ自動車「技術開発賞」を受賞した。2002年と2003年の受賞に続くもので、4年間に3回の受賞実績は、設備会社としてはまれにみる快挙だった。

「技術開発賞」の盾と賞状
リーマン・ショックによる
業績低迷。
設備事業は順調に推移し、量産部品事業も軌道に乗ったこの時期、世界的な経済危機に当社は巻き込まれてしまう。リーマン・ショックである。
2008年下期からの急激な景気落ち込みで、自動車メーカーは減産を余儀なくされ、関連企業も軒並み決算予測の大幅な下方修正を発表。長期にわたり増産を続けていた自動車メーカーは、この時点で過剰な設備を抱えることとなり、設備投資は低水準で推移。このような市場特性から、当社の設備事業の回復には長い時間を要することが予測され、会社休業・残業ゼロ化によるワークシェアリングなどが実施された。
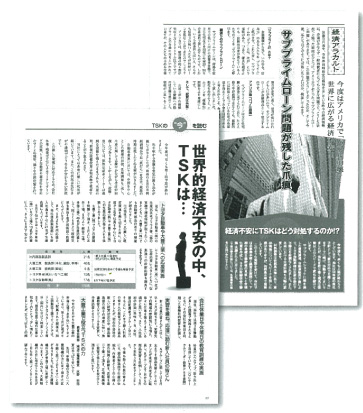
2008年8,9月号
2009年夏号
会社が直面している
状況を伝える社内報
BREAK THROUGH 大豊精機。
技術・仕事・人の変革。
2010年、このリーマンショックの危機に立ち向かうため、経営トップの強いリーダーシップにより、年初より本質的な企業改革が始まった。
「BREAK THROUGH 大豊精機」を合言葉に、部門ごとの具体的な目標を定めて、企業体質の強化が図られた。なかでもトータルエンジニアリングによる業務推進を徹底し、当社独自の「モノづくり思想の確立」に向けて第一歩を踏み出した。
また、トヨタ自動車や、大豊工業をはじめとする大豊グループ各社のご支援・ご協力により、社員の雇用を第一に、出向や転籍などの施策に注力し、社員リストラを完全回避することができたことも特筆すべきことである。
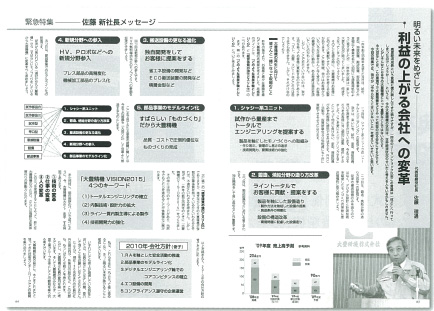
2010年度の会社方針を伝える社内報2010年初春号
トータルエンジニアリングの中枢
「T-MAC」誕生。
金型や量産部品の品質保証を目的に2009年に新設された計測解析センターが、パワーアップして呼称を「T-MAC」と改め、新たな活動を開始。この名称は、TSK(大豊精機)Measurement(計測)Analysis(解析)Center(センター)の頭文字を組み合わせたもので、デジタル情報を一元化して、当社の試作品・型・設備・量産品・試験などの全てに関わるトータルエンジニアの中枢となった。
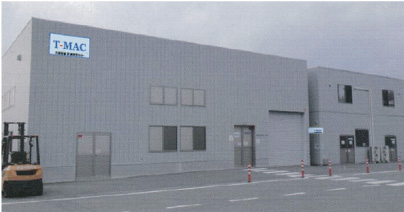
「T-MAC」誕生
ユニークなアイデアで、
次世代の設備を次々に開発。
モノづくりの現場での環境対応は、非常に重要な課題。デジタルエンジニアリングを駆使してムダのない設備づくりを進めるとともに、今までにないユニークな設備を実用化した。
なかでも2011年に完成した「エコ搬送機」は、わずかな力で移動が可能な、画期的な搬送機だ。省エネ効果が高く、ストックラックなどと組み合わせて活用することでスタッフの省人化も可能となる。
翌2012年は、プレス成形前の材料にスクラップ分散の工夫をすることで、外形抜工程時にカッター無しで加工できる「スクラップカッターレス工法」を開発。これにより、トヨタ自動車よりPJT表彰が授与された。
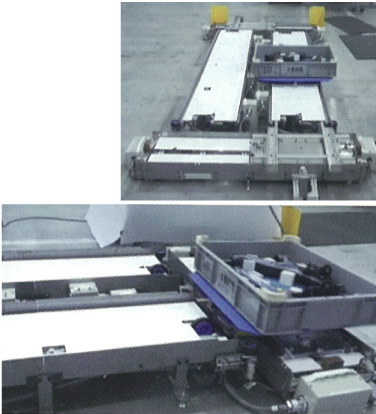
エコ搬送装置のデモ・モデル
海外事業体向けプレス自働化
設備の「RRCI活動」により
設備事業に光明。
2012年9月、鞍ヶ池工場にて、海外事業体向けプレス自働化設備のグローバル立会いが行われた。このプレス自働化設備は、競合他社との差別化・優位性を確保するため、トヨタ自動車が掲げていたRRCI活動(良品・廉価・コストイノベーション)に、全社をあげて取り組んだ成果として誕生した初号機だ。そして、今後のRRCI活動のベースとなる重要な位置づけでもあった。
こうした経緯もあり、当設備の導入先はもちろん、展開を予定している海外事業体からも現地スタッフが多数来日。国内外あわせて総勢約40名と、これまでにない大規模なグローバル立会いとなったが、この立会いにより、海外の事業体からも高い評価を得ることができた。
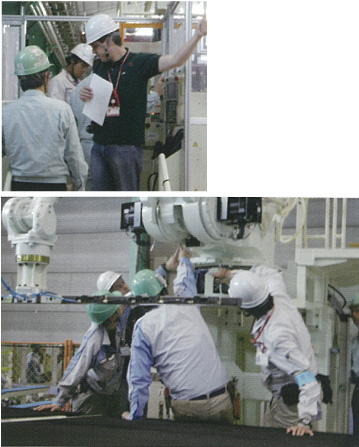
真剣に審査する参加者
T-MAC事業を、
より幅広く積極展開。
T-MACがこれまでに培ってきた3次元スキャンと計測解析技術を再編成し、社外向けサービスの展開を強化。T-MACの技術は、実体を3次元スキャニングしてCAD化、それを新規物件のデータと統合させ、整合性を検証するための一連のデジタルエンジニアリング。とくにスキャニング手法には高いノウハウが必要で、T-MACでは巨大建造物からサブナノレベルの実体スキャニングを可能とし、工業製品や設備はもとより、学術調査や教材の分野にまで活用領域を拡げていっている。
6年連続トヨタ自動車
「技術開発賞」受賞。
2002年・2003年・2006年と、トヨタ自動車「技術開発賞」を3回受賞した当社であったが、ここに来て、再び同賞受賞の栄誉を賜ることとなった。
2015年には、「電動サーボプレスモジュール」によって。続く2016年には、「ホットスタンプ用コンパクトプレス機」にて。2017年には、「コンパクト粉末成形ライン」にて。2018年には、「TWB素材突合せシステム」にて。2019年には、「コンパクト電動パイプ曲成形機」にて。
そして、2020年には、「厚物超ハイテン材アームの世界最短工程の確立」にて。
6年連続のトヨタ自動車「技術開発賞」受賞は、設備会社としては極めてまれな快挙と言える。
C+pod(超小型EV)
少量号口部品出荷開始
今までの足回り部品を中心とした量産部品の物づくりから「100年に1度の大変革」に対応すべく、多品種少量生産のトレンドをいち早く取り入れボデー部品も含む19品番の少量生産部品を立ち上げた。今まで経験したことがない多品種少量生産の新規プロジェクトを社内外一丸で達成。
本プロジェクトでは各工程を試作から号口生産まで、少量生産を考慮した工程検討を行い、約2年の歳月をかけ初品出荷となった。
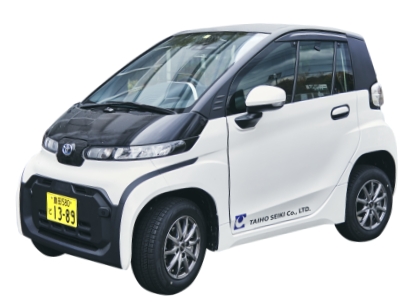
C+pod
東京2020オリンピック
聖火リレー用水素トーチ開発
トヨタ自動車様主導のもと、参画の一社として我々は水素トーチの開発に携わらせていただきました。聖火リレーのトーチは、新エネルギーとして注目される水素を利用しており、水素だけでは無色の炎となるため、炎色剤を用いて赤々とした炎を実現。ヒーターグラファイトの伝熱効果により、水素の放出効率を向上させ、高々と炎を噴き上げる等、工夫がなされています。
技術者として、今回の水素トーチは貴重な経験となりました。

聖火リレー用水素トーチ
創立50周年記念式典
2023年5月、大豊工業厚生棟体育館において、多くのご来賓の方々にご列席いただき、創立50周年記念式典を行いました。大豊精機が創立してから今までの歴史、過去5年間のスローガンに対する取り組み実績、またトータルエンジニアリングからVISION2025に触れ、「安全・品質・コンプライアンス」のぶれない軸を加速させ、100年ブランドを達成するための未来の大豊精機のあり方について語りました。
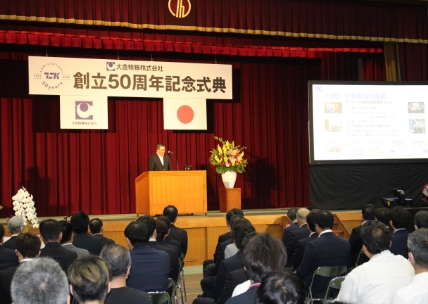
記念式典の様子